This task focuses on the development of polyphase, fault tolerant machines.
T2.1: Design of polyphase electric machines adapted to integration
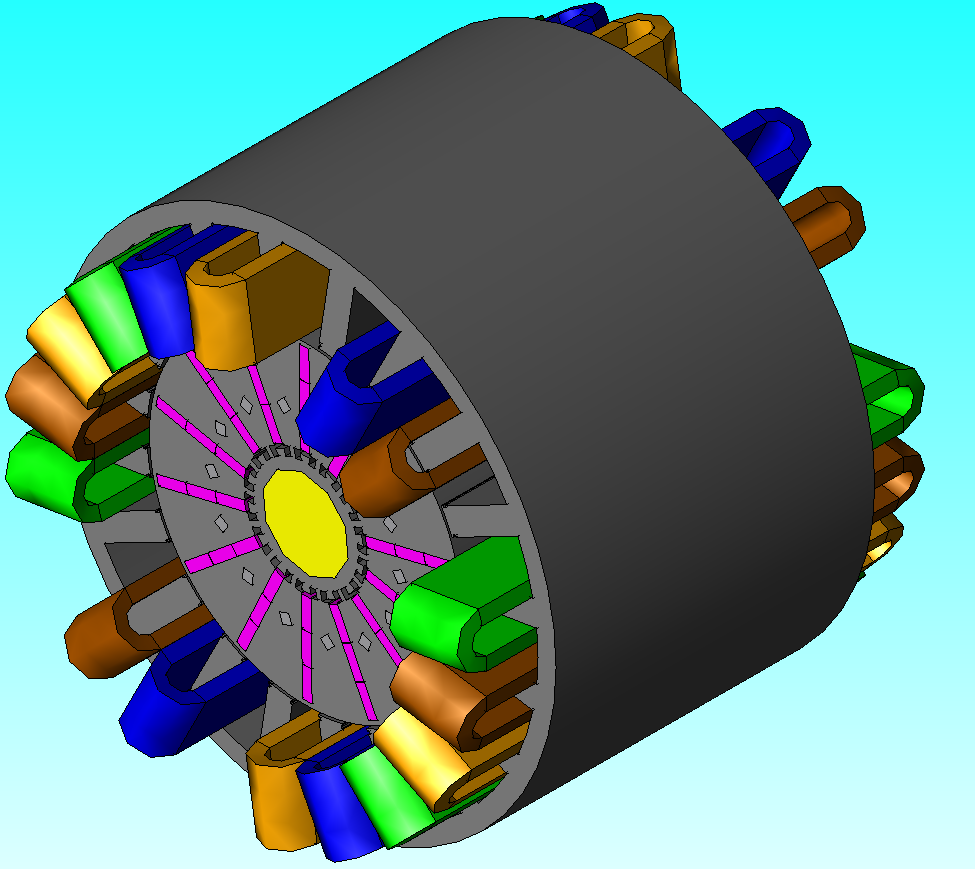
Modélisation machine sous JMAG Designer
This part aims to take into account the impact of the integration of the fast static converter in the design of the polyphase machine. It is carried out in interaction with tasks 1 and 3. The level of the bus voltages is defined as a function of the power components, the EMC stresses and the realization of the windings. The number of phases depends on the distribution of current stresses, both at the thermal and spatial levels.
The structure of the winding constitutes a compromise between simplicity and minimization of the generation of currents induced losses at high frequencies. The choice of rotor magnets integrates these temperature constraints.
T2.2: control of multi-cellular fast-component converters
This sub-task seeks the close control strategies of the switching cells of the static converter, which, using the degrees of freedom available, enable optimal power supply, the differential-mode electric circuit conventionally considered for generating the torque of the electrical machine – the common-mode electrical circuit causing EMC problems (shaft currents, overvoltages, etc.) expected as part of an integrated structure using low-loss components. This task is conducted in interaction with task 1.
Differential mode and common mode models will establish and identify the load of the static converter.
T2.3: detection and management of faults, taking into account thermal, electrical, electromagnetic and magnetic stresses
Thanks to the reduced models developed in Tasks 4 and 5, virtual prototypes will be used to test the impact of faults and reconfigurations of control on the operation of the drive. The fault detection methods derived from the established models will also be implemented in real time.
After detection and identification of a fault, reconfigurations of the control are necessary to avoid the occurrence of thermal and / or mechanical problems which reduce the functional reliability of the drive. These control reconfigurations must take account of the reduction in the number of degrees of freedom of control by the choice of appropriate strategies which, in addition, will take into account the additional constraints due to the spatial and thermal asymmetries induced by the failure. It will also be necessary to take account of the voltage and current limitations induced by the static converter and the machine.
Scientific organization of the ce2I project